Статья предназначена в основном для коллег пользующих самый доступный большинству, а также самый дешёвый способ получить давление на входе своего аэрографа – холодильный компрессор. В связи с этим возникла идея наконец упорядочить все возникающие вопросы и ответы на них в одном месте.
Итак глава первая: добыча.
Обычно в наших широтах ареал обитания диких или одичавших компрессоров довольно невелик, хотя случаются исключения. Чаще всего их можно встретить возле мусорок во дворах домов либо в подвалах, где хранят всякий хлам. Обычно они крепко прикручены к большому белому ящику, который в простонародье именуют холодильник и хранят в нём пиво. Охотиться на дикого компрессора голыми руками не выйдет, он вам просто так не дастся. А пока вы будете бегать за вооружением, дикий компрессор вполне может стать домашним, но уже чужим.
При себе надо обязательно иметь специальный комплект оружия - плоскогубцы ,отвёртки плоскую и крестик, 2 ключа на 12Х14. При обнаружении большого белого ящика необходимо внимательно осмотреть его, обычно компрессор прячется в его нижней части сзади. Если компрессор обнаружен и при вас есть необходимый комплект оружия можно приступать к добыче.
Добыча компрессора - процесс несложный, но надо к нему подойти внимательно и аккуратно, иначе в последствии могут быть проблемы. Первое что надо сделать - плоскогубцами или бокорезами откусить медные трубки, которые идут к решётке охлаждения, с припуском не меньше 10 см., а лучше – по максимуму, потом лишние трубки пригодятся (на некоторых типов компрессоров на трубках закреплена металлическая табличка с выбитыми цифрами - не выбрасывайте её, она тоже может пригодиться). Причём трубки надо именно откусить! Не в коем случае нельзя пилить, стружка обязательно попадёт внутрь, тогда ваш компрессор может сильно заболеть и умереть. При откусывании трубки заплющатся, можно этого не бояться, да и поможет не облиться маслом при транспортировке.
На этом этапе могу порекомендовать на кусочек чистой бумаги вылить каплю масла из компрессора и посмотреть его на наличие металлических частиц. Если в масле замечаются пылинки серебрянки - можно дальше не продолжать, и почтить минутой молчания светлую память погибшего агрегата.
Второе и самое главное - компрессор состоит не только из железяки, у него есть ещё один и очень важный орган - пусковое реле. Реле выглядит как маленькая чёрненькая (иногда беленькая) коробочка, отдельно прикрученная винтиками рядом с компрессором ,в неё и из неё идут проводки. Нужно аккуратно отвинтить реле от холодильника, и точно так же аккуратно отсоединить разъём который идёт от реле к тушке компрессора (это относиться к старым горшкам, у других типов компрессоров реле может быть несъёмным). Входящие 2 провода скорее всего придётся откусить, они всё равно не идут на прямую к вилке. Есть ещё один важный момент - надо запомнить или пометить в каком положении было прикручено реле, где верх и низ, оно бывает и подписано, но не всегда. Почему важно - об этом ниже.
Ну и наконец третье - с помощью 2 ключей на 12 откручиваем тушку компрессора от холодильника. Он обычно прикручен 4 болтами с гайками, через резиновые прокладочки. Желательно весь этот комплект крепежа и резинок забрать с собой, может пригодиться при последующей подготовке к работе.
Глава вторая: подготовка (одомашнивание).
Итак, вы только что добыли свой компрессор, перемазанные грязью и маслом, с исцарапанными и оттянутыми до колен руками, уставшие но довольные наконец дотянули до его дома. Теперь можно приступать к подготовке компрессора к работе. Первое что нужно сделать - контрольный пуск. Одеваем разъём реле на контакты в корпусе компрессора. Ориентируем и временно закрепляем реле на горизонтальной поверхности, можно даже скотчем приклеить. Главное - закрепить реле так ,как оно стояло в холодильнике ,оно работает на прицепе земного притяжения и нагрева пластин. Если неправильно сориентировать его, или просто бросить на весу - оно не сработает правильно, и это может кончиться фатально как для реле, так и для обмоток мотора компрессора.
Аккуратно и с помощью изоленты прикручиваем к входящим в реле проводам временный провод с вилкой. Настоятельно рекомендую замотать место скрутки изолентой, от этого зависит ваша безопасность и жизнь. Моделистов и так мало, давайте дорожить ими и собой. Заплющенные трубки нужно обжать плоскогубцами, они разойдутся в стороны и освободят проход воздуха.
Когда всё готово и закреплено - можно втыкать вилку в розетку. Обычно это сопровождается небольшим искрением и хлопком, нагрузка всё-таки немалая. Если всё в порядке - компрессор должен включиться и тихонько тарахтеть. Из трубки должен идти воздух, нужно пометить кто из них «вдох», а кто «выдох». Долго гонять не нужно, главное убедиться в работоспособности агрегата в сборе. Если не в порядке и компрессор не запускается, либо запускается и через некоторое время выключается - дело плоховато. Для небольшого обследования нужно дружить с электротехникой и тестером. Если вы с этими вещами не дружите - не рекомендую ковыряться дальше.
Ну а если дружите или имеете представление - продолжим. Надо снять разъём реле с компрессора и прозвонить обмотки мотора. Они должны звониться с небольшим сопротивлением между собой в любой комбинации. Если одна из обмоток не звониться - мы держим в руках тело погибшего агрегата. Если звониться, значит надо осмотреть и почистить реле. Аккуратно вскрыть коробочку, и мелкой наждачной бумагой подчистить контакты. Главное их не погнуть и не отломать, сильно тереть тоже не надо.
Затем собираем всё обратно, закрепляем как положено и пробуем включать вновь. Если снова не запускается или выключается – увы, не повезло… (Это при условии, что реле родное и шло в комплекте с этим компрессором. Аварийное отключение может происходить и из-за того, что мотор мощнее, чем тот, на который рассчитано реле, тогда придётся искать другое реле, а в этом поможет табличка на трубке.) Впрочем, не будем о грустном, надеемся, что всё заработало.
Теперь предстоит собрать ваш агрегат в более приспособленное и компактное устройство. Конечно, я не претендую на истину, у каждого свои возможности и средства для достижения этой цели, но изложу свой подход к сборке всего устройства. Для этого нужно посетить ближайший магазин автозапчастей, авторынок или ларёк с запчастями. Там нужно приобрести:
- Литр моторного масла для замены,10w40 или другое минеральное или полусинтетическое. обычно литр минимальная тара, но если повезёт – бывает разливное, хватит и 500 грамм. На худой конец можно смазать все скрипучие петли в доме. :)
- Резиновую армированную маслобензостойкую трубку, около метра длинной и 4мм внутреннего диаметра .Неплохо иметь с собой отрезок медной трубки от компрессора, к ней можно примерить нужную резиновую трубку.
- Металлические стяжные хомуты, 6 штук. Их надо примерять к свежекупленной резиновой трубке. Они должны быть немного большего диаметра.
- Хлорвиниловую трубку для омывателей стёкол. Они полупрозрачные, есть и армированные, но нам такие не нужны. Длину нужно выбирать в зависимости от места расположения компрессора и комфорта работы, но не менее 2 метров.
- 2 фильтра тонкой очистки – один для бензина, второй для дизельного топлива. Визуально отличаются – для бензина внутри стоит бумажная гармошка, для дизеля – внутри синтетическая сеточка.
- Тюбик маслобензостойкого силиконового герметика, лучше густой консистенции и серого цвета, более жидкий и чёрный хуже.
После приобретения всего этого надо направить свои стопы в ближайший хозяйственный магазин. В нём вы должны приобрести:
- Шнур с вилкой на конце, для запитывания компрессора в сеть. Длинной не менее 1,5 метров, желательно в двойной изоляции.
- Одноклавишный выключатель света в корпусе закрытого типа, для внешнего монтажа.
- Мебельные шурупы по дереву 3,5 х 16 или 3х16.
Теперь всю эту кучу надо объединить вместе, и мы получим вожделенный агрегат.
Первый и самый важный пункт подготовки, от которого зависит дальнейшая работа и долговечность компрессора - замена масла. Немало копий было сломано по этому поводу, надо менять, не надо, какое масло лить, а какое нет.
Мнений может быть много, но правильное - моё ! :) Дабы не возникало потом пустых вопросов типа "а у меня на подсолнечном работает и хорошо!", распишу свою точку зрения на этот момент.
Внутрь компрессора на заводе заливается чистое “веретённое” (фреонное, компрессорное - как его не называли) масло. На самом деле оно минеральное. Оно не содержит в себе никаких присадок, потому что компрессор в холодильнике работает в замкнутом и безвоздушном (безкислородном) пространстве, и не подвергается ни какому воздействию внешней среды. Когда мы начинаем его использовать в наших целях ситуация кардинально меняется. На масло начинает воздействовать кислород воздуха, микрочастицы пыли, влага и прочее. Минеральное масло довольно быстро засоряется и окисляется, теряет свои свойства. Это приводит к сильному нагреву компрессора при работе, шуму, износу поршневой системы и, в конце концов, к заклиниванию. И это притом, что масла было достаточно. Более того - в связи с небольшими связующими и смачивающими свойствами минерального масла оно будет интенсивно лететь на выход, засоряя парами воздух и уменьшая рабочий уровень в компрессоре.
Автомобильное (моторное) масло лишено большинства из этих проблем, в первую очередь за счёт содержания в нём пакета присадок компенсирующих или полностью устраняющих плохие факторы, влияющие на качество и долговечность масла. Тем более что оно рассчитано на гораздо более жёсткие условия эксплуатации, чем те, которые будут в вашем компрессоре. Я например использую моторную полусинтетику 10w40, потому что она остаётся после замены масла в моей машине. Можно использовать и минеральное, и полусинтетическое масло с другими индексами, но использовать синтетические масла не рекомендую. Во-первых дороже значительно, во-вторых они более жидкие и менее долговечные.
Надеюсь, что написал убедительно, хотя конечно найдутся неверующие, которые будут упорно заливать любое попавшееся под руки масло, ну да и флаг им.
Вернёмся к нашему железному другу. Тут возникает некоторый технический момент, а именно - какой тип компрессора попал в ваши руки. Визуально они разделяются на 2 основных типа - цилиндр и горшок (напоминает ночную вазу, прикрытую выпуклой крышкой). Первые - практически вымерший вид, применялся в очень старых типах холодильников, перестал производиться в конце 70х годов. Но если вам удалось добыть такой тип компрессора живьём - вам здорово повезло. Давление на выходе они могут дать гораздо больше остальных. Чаще всего в руки попадает именно второй тип компрессоров - горшки.
Главное для нас отличие на данном этапе - это куда менять масло. В цилиндрах чаще всего на боку корпуса вкручен огромный болт, он закрывает собой заливную горловину. Нужно открутить его с помощью гаечного ключа, слить из компрессора старое масло в какую-нибудь одноразовую посуду .Желательно замерить сколько этого масла было. В зависимости от типа цилиндра в них надо залить от 300 до 500 грамм масла. Затем аккуратно завернуть болт обратно, желательно намазав его маслобензостойким герметиком.
С горшком несколько сложнее. Из него обычно торчит 3 трубки – вдох, выдох и запаянная заливная трубочка. Масло менять желательно через неё. Для этого нам надо вскрыть эту трубочку, можно немного надрезать надфилем по кругу ниже заплющенного места, но не в коем случае не пилить насквозь. Потом по надрезу трубочку нужно надломить и полностью отломать, покачивая в стороны. Образовавшийся по краю заусенец надо слегка прибить молотком. Затем просто слить масло из горшка, наклонив его в сторону трубочек, в любую одноразовую тару. Запомните – после слива масла компрессор не в коем случае не включать!
Заправлять компрессор придётся шприцом, понемногу вливая масло в заливную трубочку, можно надеть резиновую трубку в виде импровизированной воронки. Масла в горшок требуется около 250-350 грамм. После заправки трубочку надо заглушить, иначе воздух будет уходить через неё (либо наоборот – входить мимо фильтра, зависит от типа компрессора). Можно конечно заплющить, но это не удобно, потом ведь масло придётся менять. Я рекомендую вкрутить небольшой саморезный винтик подходящего диаметра, под шляпкой которого будет резиновая шайбочка-прокладочка.
Как и в случае с маслом найдутся отчаянные или ленивые товарищи, которые будут пытаться кормить компрессор маслом на ходу, подливая его к засасывающей трубке - я крайне не рекомендую поступать так. Во-первых – масло желательно менять всё и сразу, а включать компрессор со слитым маслом – это значит убить его. Во-вторых - есть такое явление в поршневых устройствах - гидроудар. Это когда в пространство над поршнем попадает жидкость, в объёме большем, чем позволяет объём камеры сжатия. Жидкости, как мы знаем, почти не сжимаются, а мотор компрессора будет пытаться это сделать. В результате мы можем получить разрушение поршневой системы. Надеюсь, что и в этом я убедил.
И так продолжим. Теперь будем складывать всё в кучу, по приведённой схеме.

Эта схема предназначена для аэрографов одинарного действия, типа нашего любимого “Этон“ – он же – белорус, либо переделанных на однократное действие аэрографов двойного действия.
Можно конечно соединить это всё и оставить на весу, но эта конструкция будет постоянно ломаться и разваливаться. Думаю, если немного потратить сил и объединить всё на какой либо платформе или в корпусе – это будет надёжнее и доставит большее удовольствие от работы.
Не претендую на стандартизацию, но мой тип сборки абсолютно не требует применения станков, сварки или специального инструмента. Все материалы так же доступны, и стоимость их небольшая. Для самого простого и надёжного результата можно собрать конструкцию на листе фанеры или ДСП. Размеры этого листа в основном зависят от типа выбранного или добытого ресивера. Ресивер нужен для минимум двух функций – он сглаживает пульсации давления воздуха, неизбежные при работе компрессора, служит уловителем паров и капелек масла. Для недорогих аэрографов одинарного действия, к которым относиться широко распространённый “Этон“ – он же – белорус, ресивер большой ёмкости совершенно не нужен, достаточно объёма около 1-2 литров.
Как показывает практика, в качестве ресивера используют практически любые герметично закрывающиеся ёмкости – от пластиковых бутылок для напитков и пива до промышленных ресиверов от грузовиков и оборудования. На мой взгляд, использовать пластиковые бутылки и уж тем более стеклянные несколько небезопасно, эти материалы не обладают хорошей механической прочностью, и даже небольшое давление в ресивере может разорвать его при повреждении и нанести травмы. Можно конечно использовать и такие вещи как баллон от огнетушителя, но это несколько укрупняет и утяжеляет всю конструкцию.
Наиболее оптимальными ёмкостями под ресивер являются небольшие пищевые канистры для воды из полупрозрачного белого полиэтилена, либо как в моём примере – расширительный бачок от жигулей. Полиэтилен, из которого сделаны эти ёмкости, довольно толстый и вязкий, не боится механических повреждений от упавших мелких предметов и довольно долго сохраняет свои свойства. Даже если и произойдёт разрыв - он не даёт осколков или обрывков материала. Тем, кто не хочет применять такие материалы под давлением, могу посоветовать присмотреться к небольшим сварным металлическим канистрам для топлива, объёмом 5 литров.
Приспособить канистру или бачок для ресивера довольно просто – надо взять 2 трубочки, например медные, отрезанные от компрессора, длинной около 15 см каждая. Не забудьте, на компрессоре должны остаться трубки не менее 10 см длинной. В крышке канистры сверлятся 2 отверстия, в которые должны плотно входить эти трубочки. Затем с внутренней стороны крышки место вхождения трубок заливается эпоксидной смолой, полностью заливать не надо, надо оставить ещё место для вкручивания горлышка. Когда всё высыхает – нужно смазать горлышко и пробку герметиком и плотно закрутить. В этом моменте важно правильно разместить трубки – их кончики не должны быть рядом, и выходящая трубка должна быть выше входящей (как на схеме).
Теперь, когда всё подготовлено, можно прикинуть, каких размеров нужен лист фанеры. Сильно в обтяжку собирать не стоит, так будет сложнее обслуживать, да и компрессор должен иметь некоторое пространство вокруг для обдува воздухом и охлаждения. В моём случае хватило куска 30х40 см. Фанеру нужно брать толщиной не менее 9 мм, лист ДВП – 15 мм. Обрезка уголков и обработка грубой шкуркой – это уже на вкус. Но занозы в пальцах удовольствие не доставят.
По углам листа на его будущей нижней части необходимо шурупами закрепить ножки, резиновые или, например, пробки от пластиковых бутылок (хороший повод взять 4 «полторашки» пива :) ). Главное шурупами не прикрутить насквозь к полу или столу. Ножки необходимы для снижения шума при работе компрессора, предотвращают его «уползание» с места, да и поцарапать пол тоже неприятно.
Далее сверлятся 4 отверстия под крепления компрессора, болты, надеюсь, не забыли взять с собой? :) Возможно, при использовании толстого листа фанеры или ДСП может не хватить длины штатных болтов, тогда придётся купить более длинные в комплекте с гайками, в хозяйственном или авто магазине.
Самое сложное – закрепить ресивер. Устанавливать его надо первым, что бы потом не мешали остальные детали агрегата. Протыкать ресивер насквозь крепежом не стоит, здесь нужен творческий подход – например, использовать резиновую трубку или полоску, прочную ткань или кожу, перфорированную ленту для упаковки тяжёлых грузов и т.д. Один край крепящей ленты прикручивается шурупом к фанере, перекидывается через ресивер и с натягом прикручивается с другой стороны.
Компрессор закрепляется болтами, желательно трубками к краю листа фанеры, так в дальнейшем будет проще менять масло. Резьбу болтов при привинчивании желательно смазать герметиком, так они в последствии не будут откручиваться из-за вибраций. Рядом с ним шурупами привинчиваем пусковое реле, правильно его сориентировав. Дальше – выключатель света, на его контакты присоединяем реле и шнур питания. Сам шнур желательно закрепить хомутиком или петелькой к листу фанеры, так он не вырвется из выключателя.
Когда с электрической частью закончено – приступаем к монтажу остальной пневматической системы. На входе компрессора с помощью отрезка резиновой трубки и 2 хомутов закрепляем фильтр тонкой очистки для бензина. Возможно, кому-то покажется лишней эта деталь, но это ведь не дорого, и всяческая пыль не будет попадать внутрь компрессора, тогда оттуда её уже не извлечь. Главное при всех последующих операциях не залить этот фильтр маслом, он потеряет от этого свои свойства. Далее отрезком резиновой трубки и 2 хомутами соединяем выход компрессора со входом ресивера. Действовать надо аккуратно, дабы не выломать трубки из крышки. На выход ресивера так же натягиваем резиновую трубку с 2 хомутами, закрепляем фильтр для дизельного топлива. Этот фильтр можно заполнить силикагелем, тогда он будет выполнять 2 функции – уловитель влаги и переходник для закрепления резиновой и хлорвиниловой трубок. Можно конечно обойтись и без него, хлорвиниловую трубку натянуть прямо на выход ресивера, но такое соединение не будет полностью герметично и прочно, с гладкой медной трубки шланг будет срываться.
Хлорвиниловая трубка обычно меньше диаметром, чем штуцер фильтра и аэрографа, растягивается не очень хорошо, и насадить её довольно сложно. Для этого есть маленькая хитрость – кончик трубки погружается в растворитель 647 на несколько минут. Неглубоко, больше 5 мм не стоит, иначе она будет слишком гибкая, и не будет упора для её насаживания на штуцер. Желательно закрепить фильтр и хлорвиниловую трубку на листе фанеры, так она не будет болтаться и расшатывать трубки ресивера.
Ну вот практически и всё. Можно включать, послушать, как шипит воздух. Только кидаться сразу в работу не стоит, если применялся силиконовый герметик – ему надо просохнуть пару дней.
Глава третья: эксплуатация.
Здесь ничего сложного нет. Главное при эксплуатации компрессора – не допускать его перегрева. Обычно компрессор нагревается до температуры 40-45С за 25-30 минут непрерывной работы. Дольше работать не стоит, это уже может плохо отразиться на его ресурсе и качестве работы.
При дальнейшей эксплуатации, возможно, придётся регулировать давление воздуха. Например, некоторые типы компрессоров могут выдать гораздо большее количество воздуха, чем это нужно для аэрографа, либо это связано с покрасочными моментами. В этом случае компрессор будет создавать излишне большое давление в трубках, фильтрах и ресивере, да и сам он будет работать с перегрузкой и быстро нагреваться. В этом случае нам потребуется редуктор. Самое важное – редуктор в этой системе нужно устанавливать на ВХОДЕ компрессора, если он будет устанавливаться на выходе – это также будет вызывать перегрузку компрессора и его быстрый нагрев.
Устанавливая редуктор на входе, мы ограничиваем количество воздуха, проходящее через компрессор, тем самым регулируется и давление. Самым простым и доступным редуктором являются калиброванные трубочки, которые можно закрепить на входе фильтра через резиновую трубку, например от стержней авторучек, или толстые иглы от шприцов. Можно и самому насверлить разными свёрлами. Либо можно посетить ближайший зоомагазин, в товарах для аквариума можно найти очень даже подходящие маленькие краники и редукторы. И по посадочным диаметрам они как раз, и стоят копейки. В отличие от калиброванных трубочек они позволят регулировать давление в некоторых пределах по ходу работы.
Глава четвёртая: обслуживание.
Обслуживание компрессора дело не сложное, хотя для этого придётся частично снимать некоторые детали. Можно конечно и вовсе не обслуживать агрегат, но поверьте – он ответит тем же.
В обслуживание входят:
- Замена масла.
- Замена фильтров.
- Слив накопившегося масла из ресивера.
Масло, какое бы оно не было хорошее, всё равно со временем теряет свои свойства и загрязняется. В компрессоре вне зависимости от режима и количества времени его работы масло желательно менять не реже раза в год.
Для этого необходимо снять с него все трубки, вывинтить из заправочной трубочки заглушку – винтик, и наклонив компрессор вылить из него всё масло. Запомните – после этого включать его нельзя не в коем случае! Далее, как и при первой замене масла, шприцом заливаем необходимое количество масла внутрь. Пока сняты трубки – можно заодно снять старые фильтры, вылить накопившееся масло из ресивера. Вливать это масло обратно в компрессор не стоит.
Потом установить все новые фильтры на место, трубки вернуть обратно на компрессор. В этом хорошо помогают металлические хомуты, они позволяют неоднократно проводить подобные операции.
Ну вот вроде и всё, удачной работы. Думаю возникшие дополнительные вопросы можно будет разрешить на форуме.
Статью долго и муторно писал Klev.
Во время написания животные не пострадали.
Автоматический выключатель.
Для отключения двигателя компрессора при достижении нужного давления и включения после падения давления до нужной величины можно использовать самодельный автоматический выключатель на базе манометра и микровыключателя КМ 1-1 или ему подобном. Его же можно использовать для включения насоса скважины и вообще везде где нужно что-то включать/выключать в зависимости от давления.
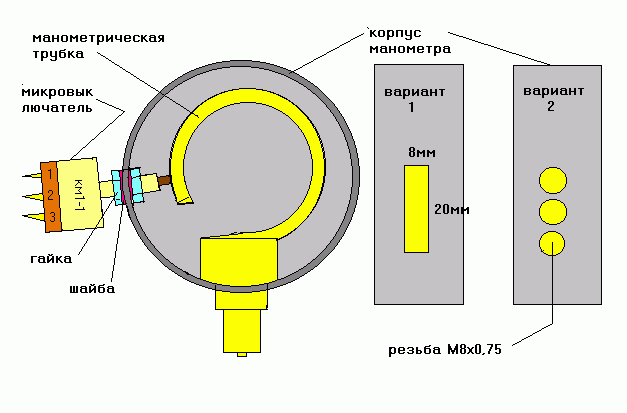
Принцип действия: при увеличении давления манометрическая трубка распрямляется и нажимает на кнопку микропереключателя - двигатель отключается. При уменьшении давления трубка сгибается и снова включает двигатель. Микропереключатель резко выщелкивает контакты и за счет этого имеет свободный ход. Если плавно нажимать на кнопку то в какой-то момент контакт щелкнет. При плавном отпускании кнопки ей потребуется некоторое расстояние до обратного щелчка. За счет этой задержки, изменяя расположение кнопки, можно добиться максимального и минимального значения давления при котором срабатывает переключатель. Например при достижении 8Кг/см2 автомат отключит, а при падении до 6Кг/см2 снова включит компрессор. Эти параметры можно устанавливать в довольно значительных пределах. Но аварийный разгрузочный клапан на рессивере нужен в любом случае.Контрольная лампа включается при выключеном двигателе, чтобы не забыть выключить молчащий компрессор после окончания работы. При трехфазном питании автомат отключает/включает пускатель. при однофазном включении необходимо пусковое реле двигателя, а реле автомата отключает общее питание двигателя. В качестве реле автомата можно использовать магнитный пускатель с катушкой на 220В или любое другое реле с достаточно мощными контактами. Если его катушка рассчитана на меньшее напряжение последовательно с ней можно подключить резистор соответствующей мощности. Первый вариант установки микровыключателя на манометр дает более точную регулировку верхнего/нижнего давления. Второй вариант менее точен, но практически это и не требуется, за то можно изменять регулировку не разбирая манометра, достаточно поднять давление до нужного и завернуть микруху до отключения, после чего законтрить гайкой. Чем ближе к концу трубки расположен переключатель, тем меньше будет разница между максимальным и минимальным давлением срабатывания. Трех отверстий обычно достаточно для любых запросов.
Конденсатор, шунтирующий катушку реле, нужен для разгрузки контактов микропереключателя.
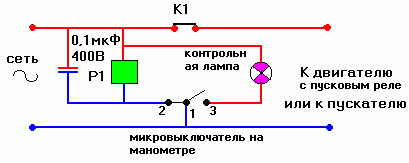
Если компрессор оборудован системой разгрузки, можно сделать автомат включающий/выключающий двигатель во время холостого хода компрессора, что облегчит пуск при питании двигателя одной фазой.
Для этого нужно немного усложнить схему введя в нее дополнительное реле и датчик давления в автомате разгрузки. Выключатель стопсигнала ГАЗ 53 ВК12Б номер по каталогу 40П-37210010. Реле Р2 нужно для инвертирования сигнала с датчика. Так -как он имеет свободноразомкнутые контакты и при срабатывании его контакты замыкаются. Если удастся найти подходящий датчик у которого при срабатывании контакты размыкаются то необходимость в реле Р2 отпадает.
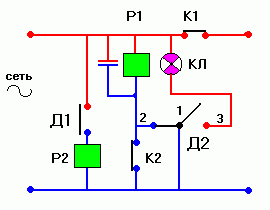
Принцип работы по этой схеме.
При достижении в рессивере давления на которое настроен датчик на манометре микропереключатель Д2 перекидывается в положение 3. и загорается контрольная лампа, но двигатель не выключается поскольку реле Р1 питается через свободнозамкнутые контакты К2- Р2 Которые размыкаются при давлении несколько большем чем то на которое настроен латчик Д2.Датчик Д1 установлен через проставку между компрессором и регулятором давления и соединен с каналом разгрузки компрессора. При работе компрессора канал 1. разгрузочного устройства соединен с атмосферой и его контакты разомкнуты. При срабатывании регулятора давления канал 1. соединяется с рессивером и давлением воздуха замыкает контакты Д1.Реле Р2 размыкает контакты К2 и отключает реле Р1, контакты К1 размыкаются и двигатель останавливаетя. Теперь если нет расхода воздуха из рессивера двигатель будет отключен. При падении давления в рессивере до значения установленного датчиком Д2, двигатель снова запустится, но компрессор все еще будет находиться на холостом ходу и не будет оказывать сопротивления пуску двигателя. При дальнейшем падении давления сработает пневматический регулятор давления, канал 1. соединится с атмосферой, контакты датчика Д1 разомкнутся и Р2 замкнет контакты К2. Вся система готова к следующему циклу. Разница давлений для уверенного срабатывания датчиков должна быть около 0,25кг/см или больше.
Источник
Компрессор для аэрографа из доступных деталей
Моделизмом я занялся недавно, и сразу для себя решил что красить модели буду обязательно аэрографом. Но одновременную покупку аэрографа и компрессора мой семейный бюджет не выдерживал, и я решил компрессор сделать самостоятельно, благо руку растут не из тазобедренных суставов, тем более примеров самодельных компрессоров в Интернете полно.
За основу решено было взять б/у компрессорный агрегат. Первым попавшимся стал компрессорный агрегат изъятый из неисправного соседского холодильника Samsung, это малогабаритный, но достаточно мощный и производительный компрессор. Еще одним достоинством этого компрессора является то, что он очень тихий, шум от его работы гораздо ниже чем от отечественных холодильных компрессоров.
Все детали компрессора смотрированы на основании из фанеры толщиной 10мм:
Рама из хромированых трубок (от старой детской коляски) и поперечного квадратного профиля (желтый) ограждают детали компрессора и служат удобными ручками для переноски.
На заднем плане виден непосредственно компрессорный агрегат. На переднем плане виден фильтр , редуктор давления с манометром, тройник с манометром и ресивер- желтый баллон из под огнетушителя объемом 2 литра.
Т.к. опыты по созданию компрессора для аэрографа из холодильного агрегата я ставил месяца два, пока пришел к такой схеме, то поясню схему компрессора, а также что и как я применил в конструкции.
Во-первых, компрессор создает давление превышающее 8 бар, и поэтой причине пришлось отказаться от соединений выполненых обычшыми шлангами - они не раз у меня лопались с громкими хлопками. Поэтому в данном варианте компрессора решил наиболее ответственные соединения выполнить либо медными трубками на пайке, либо гибкой 1/2" сантехнической подводкой в металлической оплетке.
Итак, отвод от компрессора выполнен медной трубкой 6 мм, а т.к. далее все соединения выполнены 1/2" резьбовыми соединениями я взял специальный переходник (пресс-фитинг) для подключения импортных смесителей со штуцерами в виде медных трубок:
Соединение между 6мм и 10мм трубками выполнено пайкой твердым припоем с пониженым содержанием свинца, и подмоткой тонкой медной проволокой.
Во-вторых, все холодильные агрегаты "плюются" маслом, т.е. на выходе агрегата кроме воздуха имеется и масляный туман, который недопустим для работы с аэрографом, для нормальной работы воздух надо очистить от масла. Эта задача успешно решается различного вида маслоотделителя, впрочем принцип работы у всех одинаков: пары масла конденсируются на холодных стенках резервуара маслоотделителя. Я решил совместить маслоотделитель и ресивер, так сказать в одном флаконе, а точнее баллоне- двухлитровом баллоне от использованого углекислотного огнетушителя.Для этого пришлось срезать клапан и механизм распыления, а на его место прикрутить 1/2" тройник:
Манометр я взял от сломаного ножного автомобильного насоса. Для того что бы приспособить этот манометр, контролирующий давление на выходе агрегата, пришлось просверлить подходящее отверстие и нарезать в нем резьбу, в который и был вкручен манометр. Все резьбовые соединения были уплотнены льном и масляной краской, как раньше уплотняли соединения сантехнических труб.
На этом можно было бы остановится, но я решил, что еще один фильтр "тонкой очистки" не помешает, благо в закромах был обнаружен фильтр который прилагался к стиральной машине (кажется к Аристоновской), но не был установлен, т.к. в квартире уже были установлены Honeywell-овские фильтры.Соединение от тройника до фильтра сделал 30см гибкой подводкой, она выдерживает 10атм рабочего давления.
Для регулирования и контроля давления на выходе компрессора я купил в магазине, торгующем компрессорным оборудованием, редуктор с манометром, переходник с 1/2" на 3/8" резьбу и 3/8"штуцер на шланг. Стоило это приметно рублей 400 (это , кстати , единственные затраты для этого проекта). Редуктором можно плавно регулировать давление на выходе, а манометром контролировать это давление. Единственны недостаток этого устройства в данном случае, это то что диапазон в котором обычно приходится работать на шкале манометра сужен и трудно точно выставить давленеи по манометру, я планирую заменить этот манометр на другой, с меньшим пределом.
К штуцеру подключен прозрачный шланг от омывателя стекол автомобиля (около 5 руб за метр). К дальнему концу шланга подключен мой H&S Focus. Этот аэрограф двойного действия, т.е. перекрывает воздушный поток. Для того что бы давление, создаваемое компрессором, не превысило предельного значения и агрегат не вышел из строя хорошо было бы установить реле давления, которое бы автоматически следило бы за давлением в системе. В будущем , я планирую его установить, а пока приходится контролировать давление по манометру и включать-выключать двигатель агрегата кнопкой установленой в педали под ногой.
Электрическую схему пуска двигателя корейского агрегата пришлось немного изменить, дело в том что пусковая обмотка была подключена через конденсатор 3мкФ, в отличии от привычных схем пуска отечественых агрегатов через пусковое реле. В штатной схеме, двигатель запускался не стабильно, пытался увеличить емкость конденсатора, но ситуация не изменилась, тогда я решил запустить "корейца" отечественым пусковым-реле, и получилось. Двигатель теперь запускается в 100%, не греется, только долил в агрегат немного автомобильной полусинтетики и закрыл патрубок доливки масла подходящим саморезом.
Пусковое реле:
В таком виде, компрессор уже работает 3 месяца и никаких проблем с ним не возникало. Двухлитрового ресивера накачанного до 8 бар, при отключеном агрегате хватает на 3 минуты непрерывой работы полностью открытого аэрографа при давлении на выходе редуктора около 1 бар. Герметичность такова, что накачаный до 8 бар ресивер, оставленый на ночь, теряет незначительное количество давления, которое трудно уловить на шкале манометра. Я считаю, что при минимальных затратах можно самостоятельно изготовить компрессор с неплохими показателями.
Автор:Максим Финченко
Источник
0 коммент.:
Отправить комментарий